Design, Manufacturing, Electronics, and Software integration of robotic gripper
Multidisciplinary Robotics Project
I developed a sensor-integrated pneumatic gripper, overseeing all stages from concept to manufacturing and software integration with a robotic arm.
Project Timeline

Early Stage Researching & Prototyping
Tasked to create a pneumatic gripper, I began researching pneumatics and grasping methods. Multiple ideas were considered - however a very straightforward pneumatic 'finger' design was chosen. This allowed me to focus on ensuring the pneumatic system was functional, and that the software integration was successful.
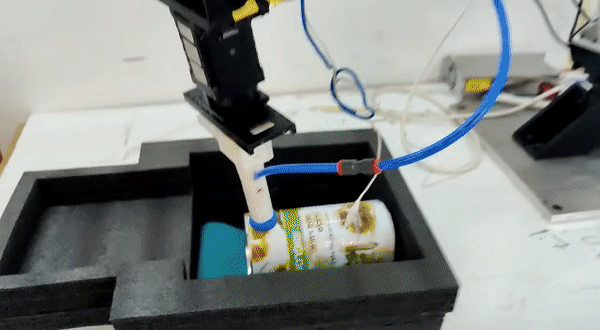
Prototype Demo
Testing proved that the pneumatic and software systems were working. It was found that although the 'finger' design was overall successful, it ran the risk of dropping an item when grasping it at a location far from its center of mass.
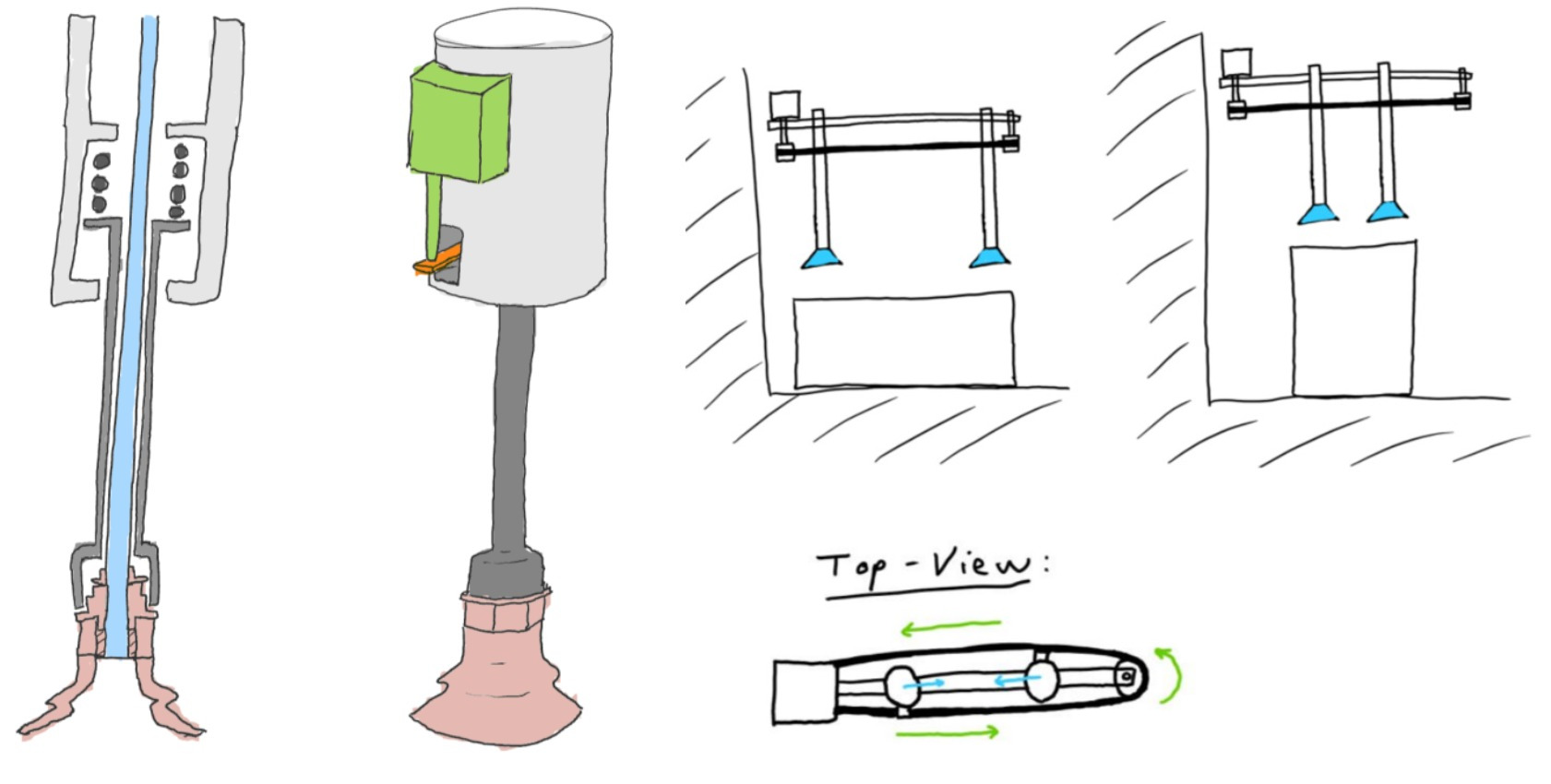
Second Design Iteration and New Details
There was now a computer vision algorithm which would detect an object, and return the best location to attempt to grasp the object. In order to deal with certain inaccuracies, I was tasked with changing the design to have the ability to 'self-correct' its pose in the event it is in the wrong location (More on this in the presentation).
Given the shortcomings of the previous design, it was decided to integrate a second "finger" into the design, which would help stabilize the grapsed object. Furthermore, in order to better understand the gripper's position relative to the grasped object, sensors were to be added to the design
After much thought, the final design of each finger consisted of a plunger-like design, connected to a linear potentiometer. This allows the gripper to "feel" what it is touching. The fingers were connected to each other via a belt-driven pulley, which allowed for change in distance between the fingers. The pneumatic system was also updated to allow for vacuum in either one or both fingers, depending on the orientation of the object to be grasped. Finally, a vacuum sensor was added to ensure adequate force can be provided by the gripper before lifting.
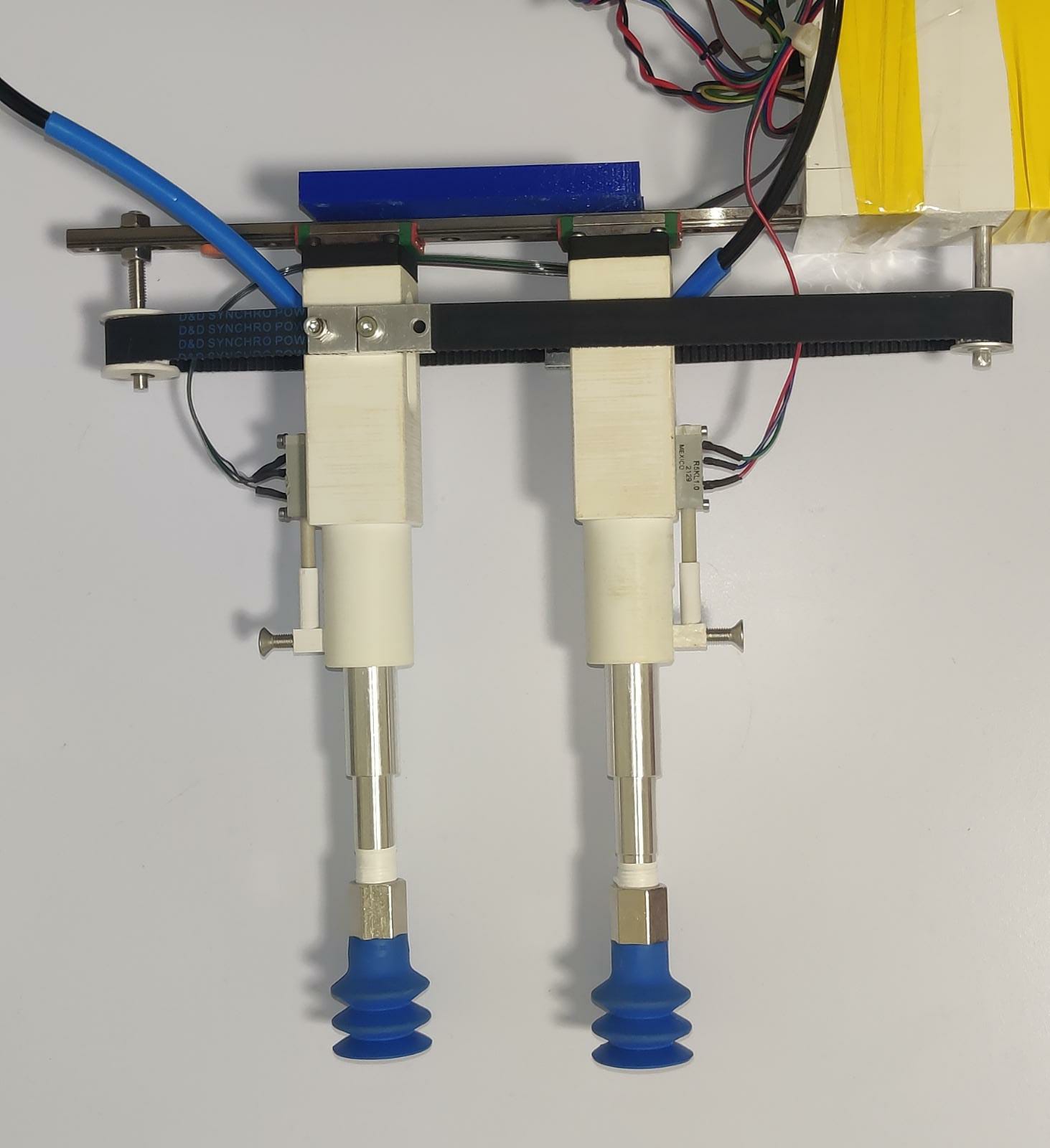
Integration
After finding the correct sensors, and ordering/3D-printing/manufacturing all required mechanical parts, the gripper was assembled. During this stage, all parts went through verification to ensure they worked correctly. This caught a few flaws in the 3D prints, which led to some small redesigns.
Eventually, all parts worked, and the gripper was ready for a test with the robotic arm.
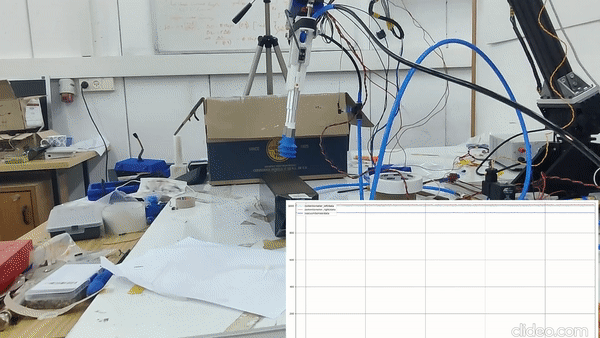
Demo of New Gripper
The testing of the gripper was successful, and the motor, pneumatics, & sensors all behaved as expected. As with any complex mechatronics project, there are things improve. However the overall goal was realized: a pneumatic gripper which has the sensor-integration necessary for performing pose-correction.
Skills Used/Learned
- Using Robot Operating System (ROS), including creating nodes, publishers & subscribers.
- Programming using Arduino and Python
- Using the ROS MoveIt package for motion planning of robot arm
- Using Rosserial to interface with microprocessor from a computer
- Experience with Linux environment
- Using SolidWorks for rapid prototyping
- Experience with software and hardware verification
- Using 3D-Printing and traditional manufacturing methods
- Experience researching & application of technologies, including sensors, electronic components & pneumatics